MTS/MSBA Workplace Safety & Health
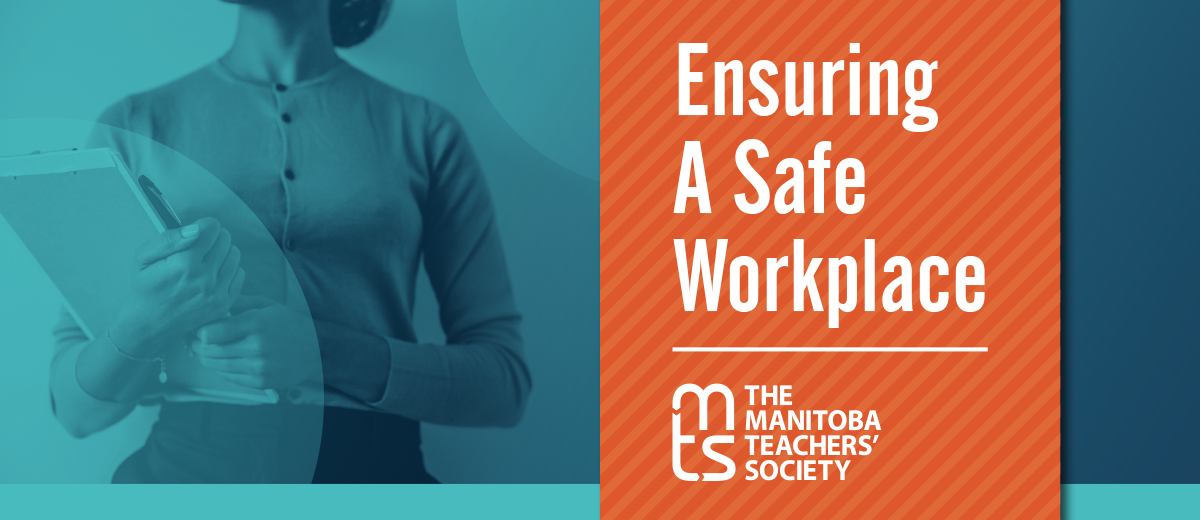
Today I had an opportunity to take part in Workplace Safety & Health training provided through Manitoba Teachers’ Society and Manitoba School Boards Association. As the head of our ICT Department, I took part to ensure I can effectively assist our staff as they work between all schools and divisional sites. This information not only informs safe work judgments for our staff but also that our tech integration is being set up and maintained in a manner that is safe for all users.
The following is a summary of my notes from the day:
The WSH Act & Regulations for Schools
- Presenter: Darren Thomas (MSBA)
This presentation goes over BEST PRACTICES with an understanding that every site is different, use your best judgment and consult your team.
Inspection Forms include:
- School Name
- Principal Name
- Contact Info
- Date
*Not all parts apply to schools so this list does not represent every component
Part 1: Policy
- Is there a current WSH policy available, signed and dated
- Is this WSH policy posted and accessible
Part 2: Safe Work Procedure
- Have required procedures been developed (reviewed every 3 years)
- Have staff/students been trained on these procedures
- Are supervisors/teachers enforcing the use of these procedures
Part 3: WSH Committees/Reps
- Is there a bulletin board to share
- Are the members/trained individuals posted
- Are you meeting regularly with the quorum
Part 4: General Workplace
- Is a copy of the WSH accessible
- Adequate air quality?
- Slip and trip hazards
- Drinking water available
- Toilet facilities are adequate and sanitary
- Thermal conditions adequate for the work being conducted
- Adequate lighting for the work being conducted
Part 5: First Aid
- Appropriate number of first aiders per shift
- First aid kits/supplies readily available
- How well stocked
Part 6: PPE
- Are the PPE requirements identified
- Is the equipment readily available
- Are workers/students observed to be wearing their PPE
- Is PPE stored appropriately
Part 7: Storage of Materials/Equipment/Machines
- Are storage systems used in the school
- Are materials stored in a condition of safe loading
- Do racking systems meet designs
Part 8: Musculoskeletal Injuries
- Which MSI risk factors are present
- List areas with MSI risk
Part 9: Working Alone or In Isolation
- Do any workers work alone or in isolation
- Has a working alone Safe Work Procedure been developed
- Is the working alone plan posted
- Is the working alone plan enforced by the supervisor/management
Part 10: Harassment
- Has a harassment prevention policy been developed
- Have the staff been trained
Part 11: Violence
- Has a violence prevention plan been developed
- Have the staff been trained
Part 12: Hearing Conservation and Noise Control
- Are workers exposed to noise in excess of 80 dBa in the school
- Tests need to be done
- Is hearing protection available for workers
- Are supervisors enforcing the use of hearing protection when and where required
Part 13: Entrances, Exits, Stairways and Ladders
- Is there safe access to and egress from all work areas
- Are muster points identified
- Are ladders present in the school
Part 14: Fall Protection
- Are guardrails in place for those who require roof access
Part 15: Confined Spaces
- Are there confined spaces
- Are workers trained in confined space procedures
- Is appropriate equipment in place
- Has an emergency response plan been developed
Part 16: Machines, Tools & Robots
- Are they used in the school
- Are procedures posted for each machine/tool
Part 17: Welding and Allied Processes
- What type of welding process is being used
- Is there any obvious damaged equipment
- Are hot work permits filled out prior to work commencing
- Are procedures posted, current, and followed
- Is there proper ventilation
Part 19: Fire and Explosive Hazards
- Appropriate number and types of fire extinguishers
- Are they mounted and accessible
- Are workers trained in the use of fire extinguishers
- Monthly inspections by staff, yearly inspection by service provider
Part 20: Vehicular and Pedestrian Traffic
- Is there a risk to the safety and health of a person due to the movement of vehicular traffic
- Is a flag person used on-site
- Are pedestrian lanes marked
Part 21: Emergency Washing Facilities
- Is appropriate emergency eyewash/shower equipment in place
- Is it accessible, clean, and operational
- Are workers/students trained in the use of this equipment
Part 35: Workplace Hazardous Products Information Systems
- Identify where they are
- Is there WHMIS training in place
- Is everyone trained
- Are the products labeled properly
- Safety Data Sheets need to be maintained for 30 years
Part 36: Chemical and Biological Substances
- Are there Safe Work Procedures for biological substances
- Are workers/operators trained
- Are there proper handling and disposal procedures in place for needlestick hazards
Part 37: Asbestos
- Is it present in schools
- Is an inventory available
- Is a control plan in place
Part 38: Electrical Safety
- Is a lock-out policy or procedure in place for electrical work
- Are they installed and protected
- Are lock-out devices available for workers
The Eleven Required Elements of a Divisional WSH Program
- Presenter: Terri Hill (MTS)
Familiarize yourself with this GUIDE
1. Policy
- Include psychological safety in your policy
2. Identifying and Controlling Hazards
- Complete a critical job inventory
- SAFE: Spot the hazard, Assess the risk, Find safer ways, Everyday
3. Emergencies
- What is an emergency?
- How should you prepare your emergency response plans
4. Roles & Responsibilities
- Internal responsibility systems
5. Inspections
- What checklist(s) are you using?
- Does your checklist include psychological and safety hazards?
6. Chemical & Biological
- This includes scent-free
7. Contractors
- Increased communication with contractors in buildings
- Have the contractors been vetted for elements like Criminal Record Checks/ Child Abuse Registry/ etc
8. Training
- WSH committee training: 2 days of paid training per year
- Job-specific training
9. Investigations
- What needs to be investigated and why?
- Accidents, near misses, violent incidents, work refusals, harassment
- There is a dedicated investigation plan
10. Participation
- All staff should be active participants in the training, conversations, reporting, etc
11. Evaluations
- Evaluate every 3 years
- Strengths and challenges
- Have you revised it to include psychological health and safety
Psychological Health & Safety
- Presenter: Irene Nordheim
Mental health is a state of mental well-being that enables individuals to cope with life’s stresses, realize their abilities, and learn well…
Mental Health Continuum self-check guide
- 500,000 Canadians, in any given week, are unable to work due to mental health problems
- 1/3 of workplace disability claims are related to mental illness
- 62% of workers say that work is their main source of stress
Stigma continues to be a barrier to conversations around mental health
There is a hierarchy of controls that can be put in place with PPE being the least you can do with eliminating the hazard as the most effective.
Best practices for workplace psychological health and safety require continuous learning, commitment, and an accountability structure.
Our goal is to help schools shift from reactive individual-focused work to proactive organization-focused work.